工程机械驱动能源的多元格局:技术演进与场景化应用
发布时间:
2025-07-02
在全球基础设施建设持续扩张的背景下,工程机械驱动能源的转型已成为行业升级的核心议题。从传统燃油到新能源技术,各类驱动形式在环保性、经济性、可靠性等维度呈现显著差异,其适用场景需结合工况需求精准匹配。
一、传统燃油动力的坚守与挑战
传统燃油动力凭借成熟可靠的技术体系,仍是重型工程领域的基石。其发动机与液压系统经过数十年迭代,在高强度矿山开采等极端工况下稳定性突出,大扭矩输出特性完美适配重载需求,且具备-30℃至50℃的宽温域适应能力。全球密集的加油站网络支持5-10分钟快速补能,初始购置成本也具竞争优势。然而环境污染问题日益严峻:柴油机排放的氮氧化物(NOx)和颗粒物(PM)占非道路机械污染总量60%以上,仅20%-30%的热效率意味着70%以上能量被浪费。随着国四排放标准实施,尿素添加系统的运维复杂度增加,长期维护成本持续攀升,85分贝以上的噪音振动更影响操作舒适性。
二、纯电驱动的环保革命与技术瓶颈
纯电工程机械以零排放和低于65分贝的静音特性,成为城市隧道、室内场馆等敏感场景的理想选择。电动机92%-98%的能源转化效率带来显著经济性,如博雷顿电动装载机年均运营成本较燃油机型降低21.97万元。结构简化使故障率下降40%,而智能变频控制技术实现功率与负载的精准匹配。但电池成本占比高达40%-50%,导致初始价格超出燃油机型50%以上。低温环境下电池容量衰减30%,1-2小时充电时间制约连续作业效率。380V工业电网依赖限制偏远地区应用,三电系统(电池/电机/电控)兼容性不足与电池回收技术缺失,仍是产业化关键障碍。
三、混合动力的过渡平衡之道
混合动力技术通过电机低速驱动与发动机高速协同的智能策略,实现燃油消耗降低25%-40%。再生制动等能量回收技术转化效率达35%,灵活的运行模式切换满足排放限值区域作业需求。电动机的低磨损特性使维护成本优于传统机型。然而多动力源集成推高制造成本,购车价格增加30%-50%。并联式结构需复杂离合器与变速器,控制策略开发难度大。电池容量限制纯电续航里程,超级电容器过热风险影响系统稳定,机械能→电能→机械能的二次转换更造成15%的能量损失。
四、天然气动力的清洁化实践
天然气发动机凭借减排90%颗粒物、CO₂排放较煤电低50%的环保优势,成为过渡期重要选择。LNG燃料成本仅为柴油70%,燃气电站3年建设周期显著快于传统电站。发动机磨损率低令大修周期延长至12000小时,模块化设计适配发电机组至挖掘机多类设备。但加气站覆盖不足使偏远地区补能耗时增加50%,能量密度仅柴油25%导致储气罐体积庞大。甲烷泄漏风险需专用探测设备管控,燃料特性还造成发动机功率下降10%-15%。
五、氢燃料电池的零碳攻坚
氢燃料技术以全程仅排放水、能量密度120MJ/kg(百倍于锂电池)的颠覆性优势,成为零碳战略的核心载体。3分钟快速加注特性契合工程机械连续作业需求,40%-60%能量转换效率在热电联产模式下可达80%。欧盟50亿欧元专项补贴凸显政策支持力度。但储运环节能量损耗严重:氢气压缩损失13%,液化损失40%。单座加氢站建设成本超200万美元,全球总量不足千座。铂催化剂占系统成本30%,电解槽60%的制氢效率制约"绿氢"发展,高压储氢罐的氢气脆化金属风险更需材料学突破。
技术路线的场景化抉择
矿山开采场景中,传统燃油动力链的可靠性不可替代,混合动力可辅助节能;城市基建领域需纯电设备主导低排放区,配套充电网络是落地关键;港口物流场景适合氢燃料重载机械与固定式加氢站形成闭环;偏远工地则依赖LNG动力经济性与移动式加注设备。驱动能源的竞争本质是能源密度、基础设施、全周期成本的动态平衡。当前技术迭代呈现多线并进:锂电池成本持续下探(2025年预计$80/kWh)、氢燃料商业加速(2030年绿氢目标$2/kg)、混合动力控制智能化突破。未来十年,基于工况大数据的能源配置算法将重塑工程机械产业竞争力。
在工程机械驱动能源绿色转型的浪潮中,亿控的纯电驱动轮技术正成为工业与农业智能装备的革新力量:其TEC410卧式舵轮凭借±0.05mm定位精度与IP67防护等级,在汽车零部件智慧工厂中实现AGV毫米级精准搬运,集群日均减碳4.8吨;而专为农业场景研发的TEC1450P大扭矩驱动轮则以2000N·m峰值扭矩和自清洁沟槽设计,助力播种机器人在东北水田提升35%作业效率,彻底终结燃油消耗。两款产品深度融合纯电驱动核心优势——运行噪音<76分贝、能效转化率>95%,以零排放动力为智能装备提供静音、免维护的绿色心脏,持续赋能产业可持续发展。
更多资讯
微信:13802232914
邮箱:jimmy.tang@shtongpu.com
地址:江苏省南通市海门区滨江街道滨港大道2699号内63号楼
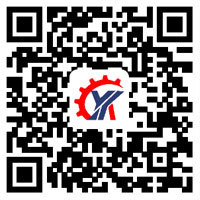
扫一扫 关注亿控智装备