车间介绍

生产能力与完善的供应链体系
我们工厂面积超10000平米,年产电机,驱动器,舵轮总量可达10万台。公司与100+家核心供应商构建战略协作网络,关键零部件库存周转率精准控制在7天以内,支撑全球订单准时交付率突破99.2%。通过MES数字化系统,实现从原料采购到成品出库的全流程可视化管控,确保柔性化生产与定制化需求的快速响应,为市场提供高效稳定的供应链保障。

精密加工车间
车间部署多台五轴CNC加工中心及三坐标测量仪(精度±0.01mm),专注PLT驱动轮核心部件的高精度加工,包括行星齿轮、谐波减速器壳体等关键组件的加工和检测。齿轮齿面加工精度达ISO 5级,使组件在重载AGV及特种车辆场景下的耐久性超20,000小时,满足高强度工业应用需求。

装配车间
由10+名平均从业经验超10年的资深技师主导装配流程,严格执行ISO 9001标准化作业规范,涵盖电机-减速机同轴度激光校准、制动器动态间隙微调、编码器信号耦合度测试及扭矩传感器线性标定等核心技术环节。每台驱动轮完成装配后均需通过100%在线质检,确保一次装配合格率高达99.8%,从源头保障产品可靠性。

测试车间
车间配置高低温循环箱(-30℃至+70℃)、盐雾试验机(1000小时中性盐雾测试)及动态负载测试平台等专业设备,系统性执行72小时连续满载测试(额定负载150%冲击,电流波动<±5%)、温升-效率曲线分析(电机温升≤65K,能效≥92%)、IP65防护等级验证及噪音检测(空载≤55dB,满载≤68dB)等12项全维度性能验证。所有驱动轮,驱动器等产品需符合严苛质量标准后方可出厂交付,确保为客户提供高可靠性的产品保障。
微信:13802232914
邮箱:jimmy.tang@shtongpu.com
地址:江苏省南通市海门区滨江街道滨港大道2699号内63号楼
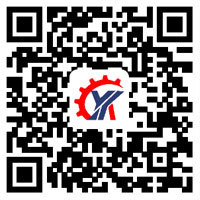
扫一扫 关注亿控智装备